Blog
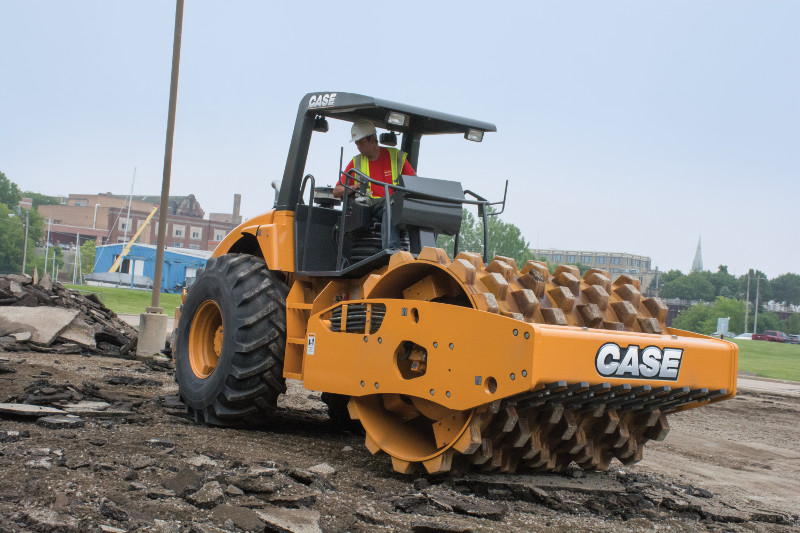
A Few Minutes of Equipment Inspection Each Day Can Prevent Costly Downtime
April 24, 2018Your crews depend on your equipment to ensure that jobs are completed safely, efficiently, and in a timely manner. So what can really throw a wrench in the gears of getting things done? Equipment down time. Even top quality equipment from CASE can experience downtime when proper maintenance and servicing is overlooked.
Thankfully, equipment operators can prevent downtime, extend service life and ensure more efficient operation with just a few minutes of preventive inspection both pre- and post-operation. Those few minutes of investment in inspection are the absolute key to preventing costly downtime events.
Here are a few of the most important items we recommend for regular inspection.
Pre- and Post-Operation Equipment Inspection Checklist
- Check fluid levels – engine and hydraulic oil, diesel and diesel exhaust fluid (DEF), and coolant. Fluids are the lifeblood of each machine and require specified levels to operate properly. A sudden drop in fluid levels may point to any number of problems with the machine that require immediate attention (blown hoses, leaking filter, etc.).
- Check fan belts, alternator belts, etc. – A worn and frayed belt is relatively easy to replace. Attention to a belt’s wear can prevent unplanned downtime that would occur if the belt snapped while on the job site.
- Check tires, rims or undercarriage for damage or abnormal wear and clear away debris. Think about it like what it feels like to wear shoes that fit poorly or have a floppy sole – machines with messed up tires and undercarriages are incapacitated in the same way. A machine can be hobbled by the inefficiencies of the tires or tracks it sits on. Identify and report any damage or potential damage.
- Clear any accumulated debris from around the radiator and other engine components. The engine is made of moving parts and belts that generate heat and friction. To deal with properly dispersing that heat, systems designed to cool the engine compartment require room to breathe. It’s important to check and remove any clutter that may have found its way into the engine compartment.
- Check the fuel, oil, air and other filters for signs of damage or leaking. Filters are often a quick and easy item to replace – and operating with properly working filters can prevent any number of problems with the machine.
- Identify greasing points and frequency. Each machine is basically formed from giant pieces of steel working together – so keeping the machine properly greased is critical to reduce friction. Proper greasing can also help keep out moisture and abrasive materials from the jobsite that can work into joints and friction points.
- Check auxiliary hydraulic connections and pressure. Simply check the integrity of the coupling structure and that it hasn’t been damaged. Keep in mind, also, that newer equipment often includes pressure relieving quick disconnects – take the time to relieve the pressure when disconnecting attachments.
- Check for leaking or pooled fluid around and under the machine. This is one of the most obvious indicators of a potential problem. Finding the source of the leaking fluid is critical. Also be sure to replace the lost fluid before operating the equipment.
- Inspect the operator compartment and clear away any debris, trash, or other obstructions. Clutter is a distraction – and anything in the cab that ultimately prevents the full range of controls from being engaged is a hazard to operation.
- Inspect the attachment mount-up to ensure proper connection. This includes checking that the coupler is flush and fully engaged (either via manual or automatic/hydraulic means), and that the hydraulic hoses (and electrical connections, if applicable) are properly connected.
- Familiarize yourself with the control style and change as needed. Most of today’s machine’s come with rather simple pattern selectors that allow the operator to use the control pattern that they are most familiar with.
- Identify auxiliary/attachment controls. Each type and style of machine controls attachments differently – operators should identify how to properly work their attachment prior to attempting to use it.
- Start the engine and review console indicators and warnings. Today’s machines are built to give the operator more feedback on the workings of internal systems than ever previously available. Take note of any flashing symbols or warning lights, check the owner’s manual and consult with maintenance staff prior to operation.
- Review all external surroundings from the cab. Know your work site, and the people and structures that exist inside your working envelope. This will ensure optimal jobsite safety and productivity.
This is certainly not an exhaustive list for inspection – your particular tasks and usage habits will lead to ideas of items you should add to the list. But starting with this list will go a long way in preventing costly downtime due to equipment issues.
Ben Franklin (who didn’t live very far from our area, by the way) was certainly right with his wise adage: “An ounce of prevention is worth a pound of cure.” Your equipment inspections can have a huge impact on preventing issues. If you have more questions about preventative maintenance, want to talk about equipment sales or rentals, or inquire about our service programs, we’d love to talk! All of the store locations and contact information for Eagle Power & Equipment can be found here.